Thailand
Displaying present location in the site.
Smart Manufacturing
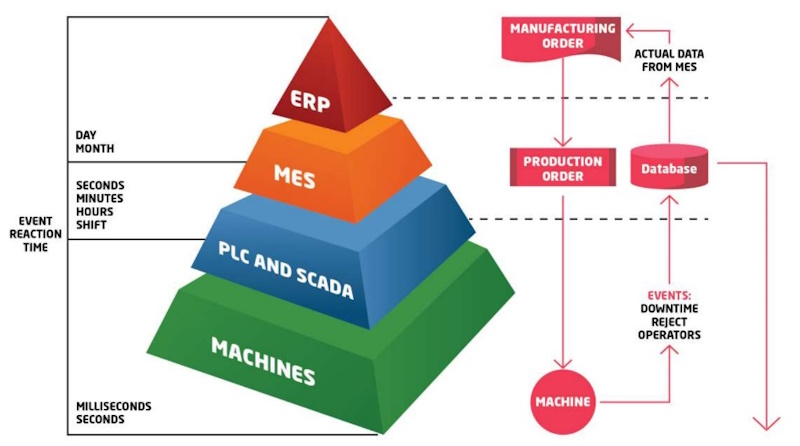
About Smart Manufacturing
Smart manufacturing, also known as Industry 4.0, refers to the integration of advanced digital technologies and data analytics into the manufacturing process. NEC Corporation(Thailand)Ltd. aims to enhance efficiency, productivity, and flexibility in production systems. Here are some key aspects of smart manufacturing:
- Connectivity
- Data Analytics
- Robotics Process Automation (RPA)
- Predictive Maintenance
- Cybersecurity
- Customization
- Supply Chain Optimization
In a summary, smart manufacturing transforms traditional factories into agile, data-driven ecosystems, leading to improve productivity, cost savings, and sustainable practices.
Data Science
A data science platform integrates various tools and functionalities to support data scientists, analysts, and business users.
Key features include data preparation, model building, visualization, collaboration, and deployment.
Here are some key aspects of data science platforms:
Data Integration and Preparation:
- Import, clean, and transform data from various sources.
- Handle missing values, outliers, and data quality issues.
Data Analysis (DA):
- Visualize data distributions, correlations, and patterns.
- Identify insights and potential features.
Model Building and Training:
- Develop machine learning models using algorithms.
- Tune hyperparameters and evaluate model performance.
Model Deployment:
- Deploy models for real-world use.
- Monitor model performance and updates.
Collaboration and Version Control:
- Enable teamwork, code sharing, and version tracking.
- Facilitate collaboration between data scientists and business stakeholders.
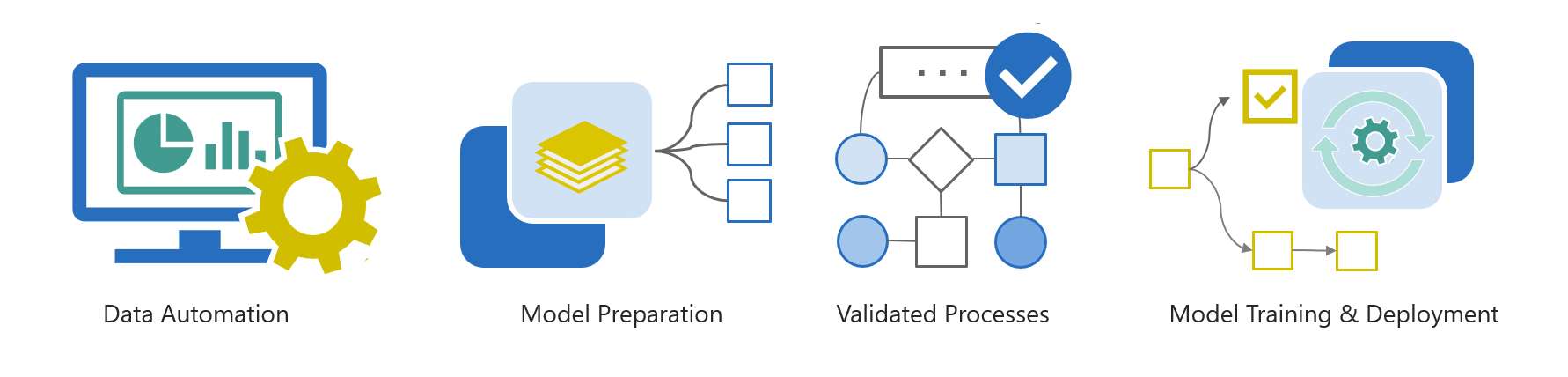
Try AutoML for Predictive Maintenance
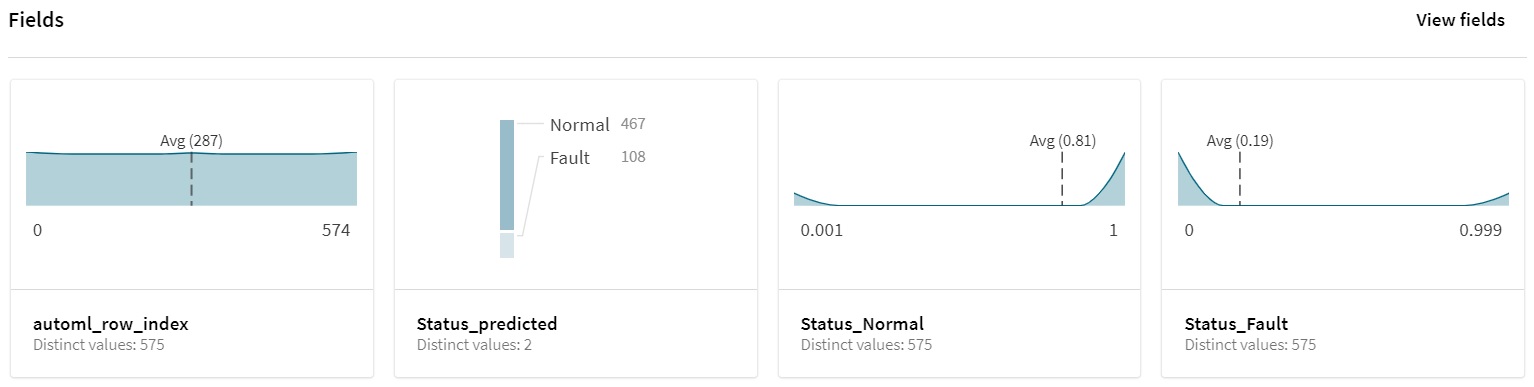
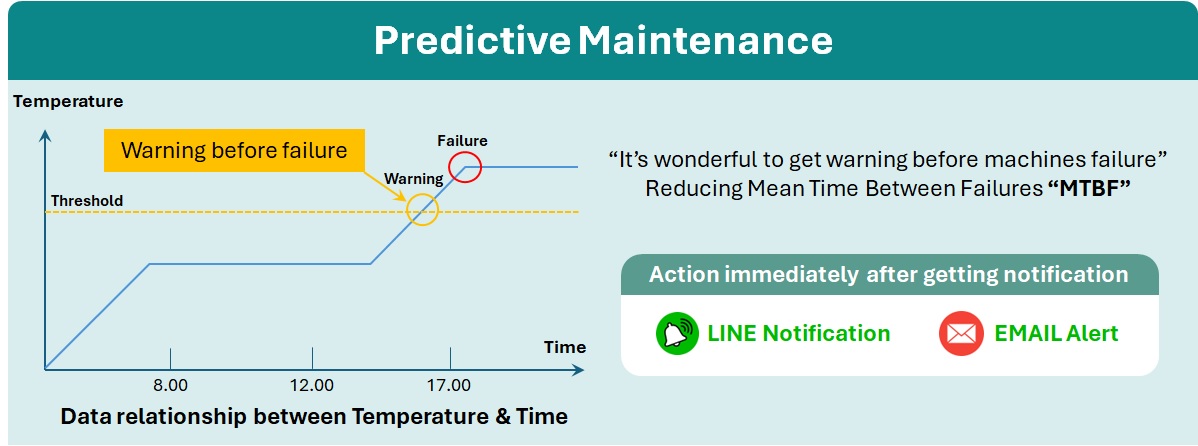
Data Analytics – Cloud Business Intelligence (BI) & AutoML
Business Intelligence is a technology-driven process for analyzing data and delivering actionable information that helps executives, managers and workers make informed business decisions
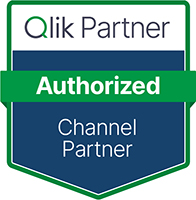
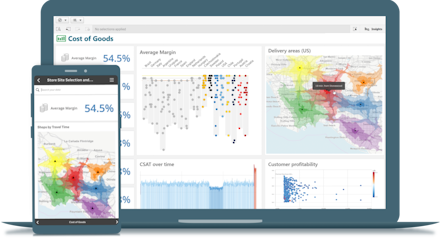
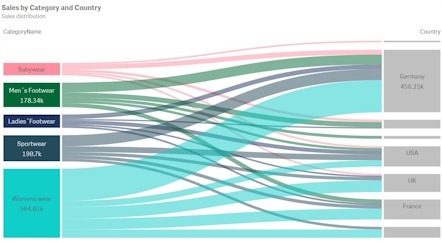
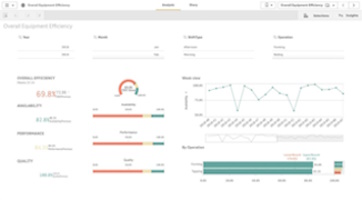
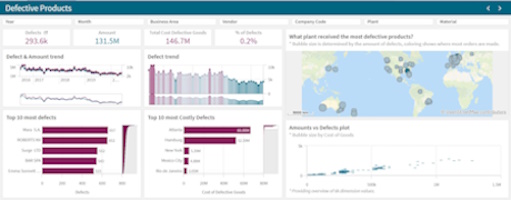
Data Integration
Data integration is the process of combining data from different sources into a single, unified view. Integration begins with the ingestion process, and includes steps such as cleansing, ETL mapping, and transformation
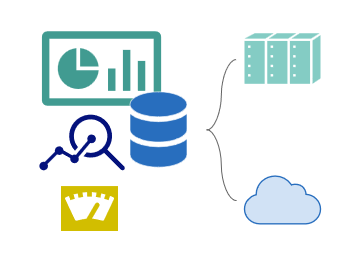
Data Integration for Enterprises
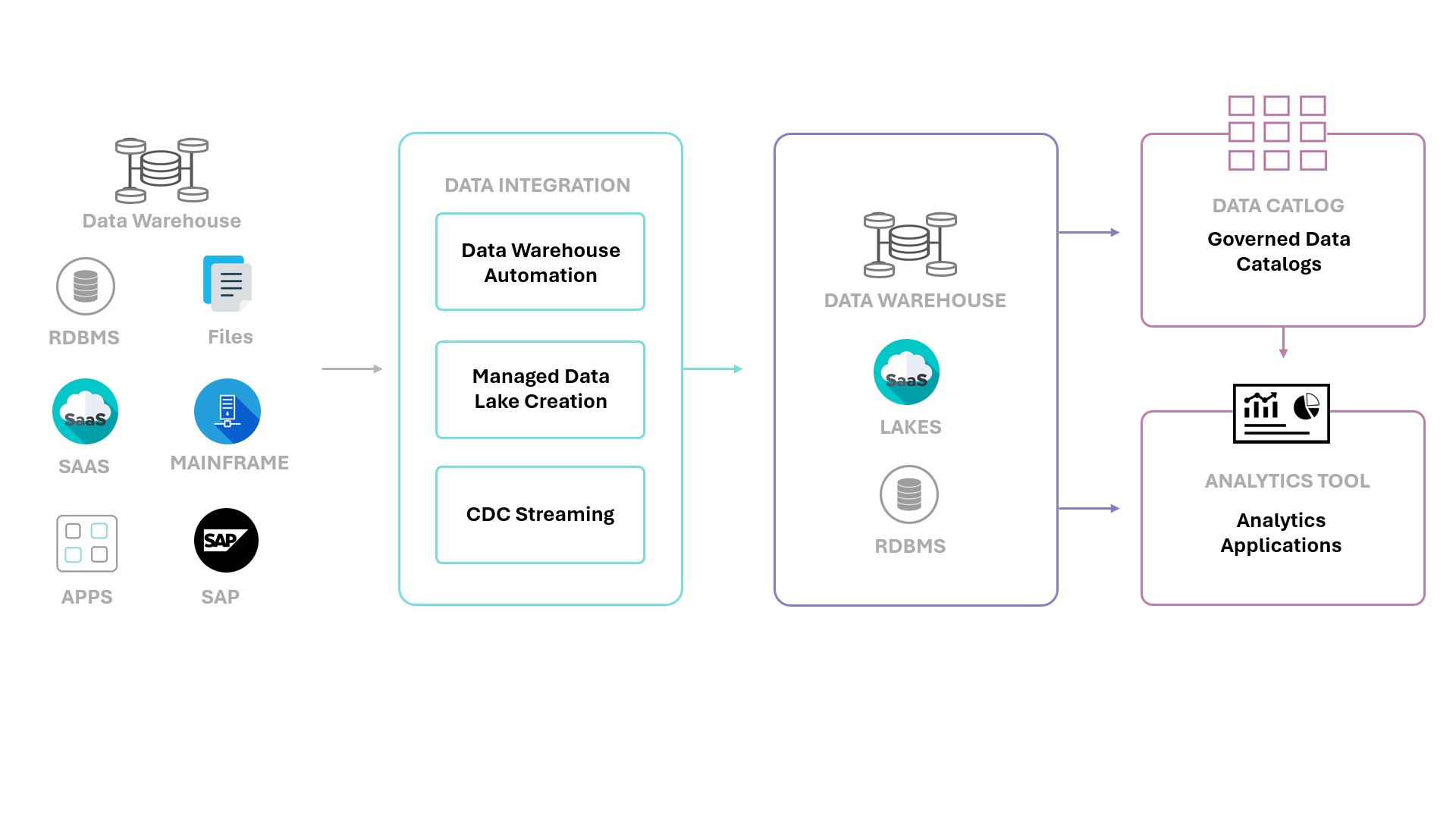
Manufacturing Execution System (MES) | MES For Industry 4.0
Manufacturing execution systems (MES) are computerized systems used in manufacturing to track and document the transformation of raw materials to finished goods. MES provides information that helps manufacturing decision-makers understand how current conditions on the plant floor can be optimized to improve production output. MES works as real-time monitoring system to enable the control of multiple elements of the production process
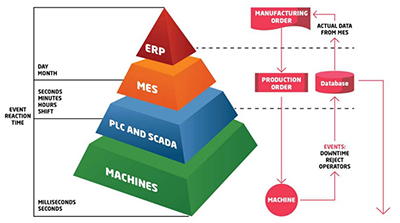
Case Study
Production Monitoring Project in
The Automobile Industry
Challenges:
- Untraceable of the production performance and quality
- No real-time machine monitoring system for status and performance
- No digital information for analytics
- No connection to industrial robots
Solutions
- Monitoring system for production (OEE, productivity, and Andon)
- Tool life tracking and notification to change a new tool
- Architecture design for data collection, network, server, and IoT devices to connect industrial robots
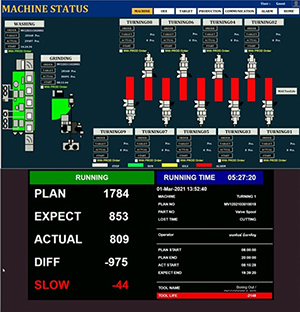
SCADA
SCADA (supervisory control and data acquisition) is a category of software applications for controlling industrial processes, which is the gathering of data in real time from remote locations in order to control equipment and conditions.
Sensing
Sensing level is closest to your factory floor and assets and includes sensors and valves. The sensors and other IoT devices you use on the factory floor collect data from manufacturing processes and transmit the data to a controller or subsystem.
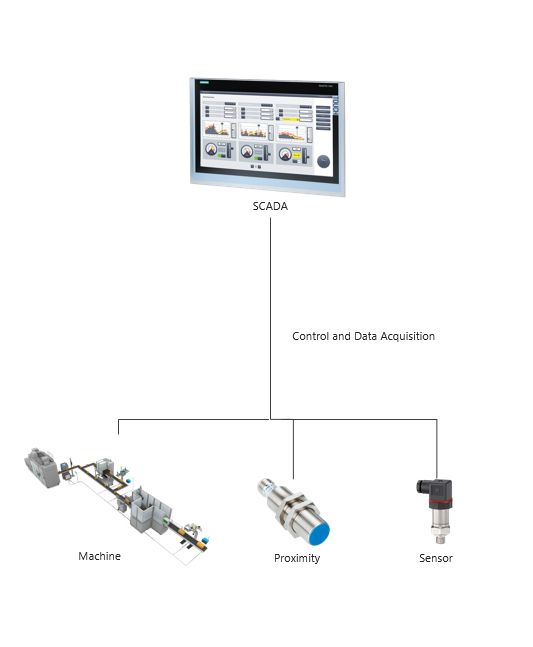
Case Study
Digital Kaizen and Line Monitoring Project in
The Food and Beverage Industry
Background:
The customer was unable to visualize data on the factory's production lines, resulting in a large amount of waste. In order to reduce waste, the factory needed to be operated efficiently and rationally
Challenges:
- No system to call a foreman/leader to solve a problem in the production line
- No historical production data for analysis
- No system to find a person who weighed less/over in a weighting process
- No takt time or cycle time for tracking
- No alert system to notify when the waste is over the target amount
Solutions
- Andon system to call a foreman/leader to solve a problem promptly
- System to monitor real-time and historical who weighted over/lower daily by collecting 5 weighing scales machine data
- Alert system to when waste accumulates more/less than the target amount
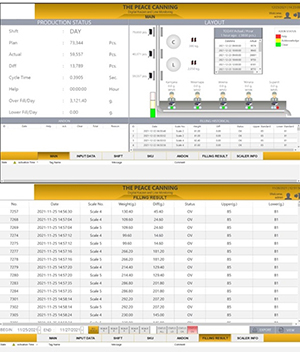
NECARE
- Phone Number:+66 (02) 204 9600
- Email Address:necare@nec.co.th
- Address:3 Rajanakarn Building, 22nd Floor,
South Sathorn Road, Yannawa, Sathorn,
Bangkok 10120, Thailand