Thailand
Breadcrumb navigation
Pioneer Manufacturing (Thailand) Co., Ltd.
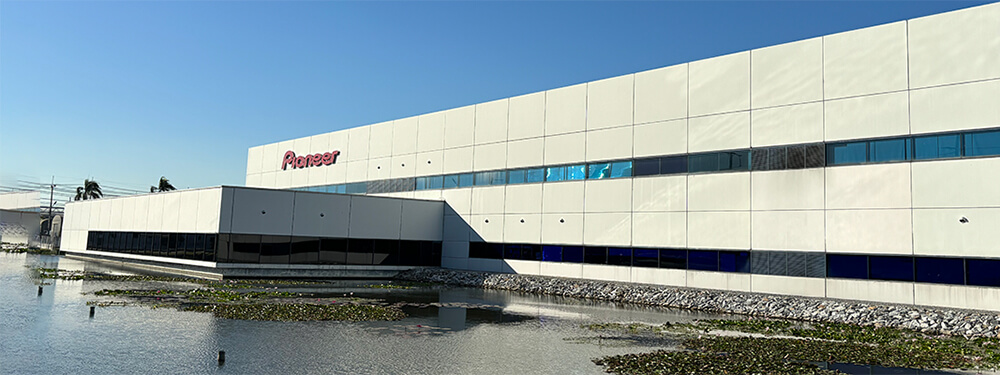
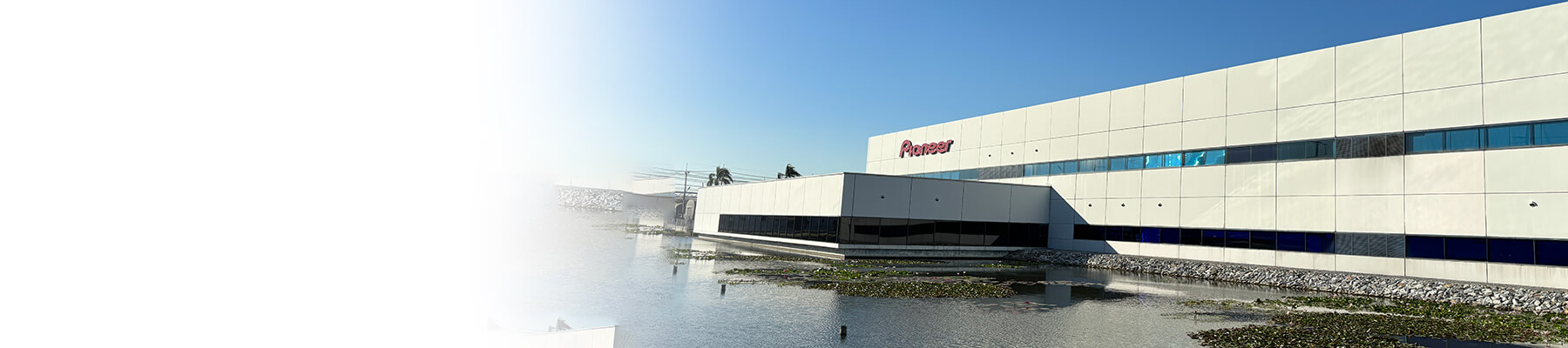
Leveraging a Low-Code Development Tool to Cut Costs and Build Subsystems: Streamlining Slip Processing and Achieving Fivefold Efficiency through Digital Transformation
- Industry:
-
- Manufacturing
- Region:
-
- Asia Pacific
- Products:
-
- Software
- Others
- Solutions:
-
- Others
Case Summary
Issue Background
- The core system had become outdated, however, from a cost and personnel perspective, it was crucial that the existing system was kept running for the time being.
- The process demanded significant quantities of paper and manual labor, prompting the need for a more streamlined and paperless approach.
- To maintain agility in the face of environmental changes, it was vital that future updates and modifications to the system could be handled by the client.
Achievements
Enabling Agile Development On-Site Using a Low-Code Development Tool by Customer
We have enabled operational improvements without altering the core system by utilizing a low-code development tool to build the necessary subsystems for improving on-site business. As a result, we have empowered the client's staff at each site to swiftly and adaptively execute modifications and advancements in response to business environment shifts, through a gradual transfer of skills.
Automation Empowers Human Resources to Engage in Value-Adding Tasks
We have helped the client to systemize their material receiving and invoice verification processes, which were previously reliant on manual checks, in an effort to conserve labor. This optimization has led to a significant reduction in the time required for invoice processing, from 500 hours per month to just 100 hours per month. As a result, the client has been able to reallocate our human resources to tasks that add greater value to their business.
Contributing to the Environment by Reducing Waste through Paperless Operation and Inventory Optimization
Realization of paperless operations, eliminating the need to print as many as 5,000 invoice PDFs each month by our development of subsystems. Furthermore, the client's enhanced ability to perform inventory management has curtailed waste.
Solutions
Developed subsystems using the low-code development tool ‘TALON’, without making modifications to the core system.
Automated manual tasks and achieved paperless operations by utilizing RPA and AI-OCR.
Order data inputted into the core system was cross-referenced with the QR codes on delivered items. This process enhanced the efficiency of receipt inspection and strengthened the integration with the core system. In addition, a new system was introduced that employs AI-OCR technology to convert invoice information into data, which was then matched with the order data in the core system. Through cost-effective, low-code development, we realized operational efficiency without the necessity for costly alterations to the core system.
Case Details
Background and Issues Before Introduction
Enhancing Operational Efficiency Without Altering an Outdated System
Pioneer Corporation, a global trailblazer, has consistently been at the forefront of the automotive electronics industry, introducing numerous world and industry-first products and services whilst utilizing innovative and unique ideas and cutting-edge technology. Lately, Pioneer has broadened its scope beyond just hardware. They now offer solutions integrated with the cloud, harnessing a vast array of mobility data, camera images, and location information. Their goal is to contribute to the realization of a safe and secure society in motion.
Within the Pioneer Group, Pioneer Manufacturing (Thailand) Co., Ltd. (hereinafter 'Thailand Plant') takes the lead in producing car navigation systems and car audio products, standing as the group’s most significant production hub. This plant is set to celebrate its 30th anniversary in 2024.
Since its inception, the company has been utilizing a core system. This system, introduced at the time of establishment, has undergone numerous modifications over time. However, this system, like the one at the Japanese headquarters, had become obsolete. This prompted plans for system renewal. Unfortunately, the cost of renewing the system at the headquarters exceeded expectations. As a result, the Thailand Plant was excluded from the renewal plan.
Therefore, the plan for business efficiency improvements, which was based on system renewal, was put on hold. It became necessary to rethink the plan, now with the premise of continuing to use the old core system.
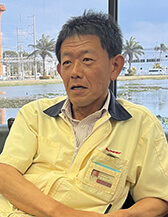
Production Control & Procurement Management Division
Senior General Manager
Mr. Yoshihiro Wada
The following operations required streamlining through systemization; the first of which was receipt inspection for parts and other delivered materials. Until the current project started, whenever materials were delivered, the person in charge would manually check the order information in the core system one by one. If the information matched, it was entered into the core system and used as inventory information. "This process took a lot of time and space in the warehouse," says Mr. Yoshihiro Wada, who is in charge of production and logistics management at the Thailand Plant.
On the accounting side, the invoice checking process was particularly labor-intensive. Every month, about 5,000 invoices would arrive in PDF format. Each one had to be printed out and manually checked against the order information in the core system by the person in charge.
"The entire operation required about 500 hours each month. In addition, human errors were frequently occurring in the reconciliation process,” confides Mr. Eitaro Endo, general manager of the Administration & Accounting Division.
The improvement of such process inefficiencies needed immediate action.
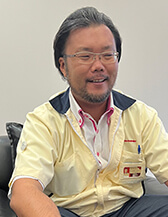
Administration & Accounting Division
General Manager
Mr. Eitaro Endo
Key Points for Selection
Solving Issues with Subsystems that Can Be Developed Without Incurring Large Costs
Mr. Wada said, "We reached out to NEC Thailand, a company we had always collaborated with and consulted on systems with, to explore the possibility of developing a QR code-based receipt inspection system for this project as well.”
Shigeru Matsubara from NEC Thailand, who understood the system’s situation at the Thailand Plant, proposed the development of a subsystem using TALON. His proposition was based on several considerations: the core system couldn’t be replaced due to the high cost of modifications; the client had an IT division capable of developing the system independently, but they were extremely busy; and the system needed to be flexible enough to adapt to a rapidly changing environment.
TALON, utilized by NEC, is a low-code development tool that fundamentally allows users to build systems by modifying various settings in a browser, with some elements necessitating programming. It provides user interfaces for displaying individual reports, comprehensive statements, calendars, graphs, and Gantt charts. Each user has the ability to tailor these functions to their own preferred user interface.
"Initially, our role was to provide support during the system development phase. However, the pivotal aspect of our proposal was the gradual skill transfer to the client's team, empowering them to eventually assume full control and independently conduct system development." (Matsubara)
NEC Thailand’s proposed receipt inspection system automatically aligns the QR codes on delivered materials with the order data in the core system. This updates the inventory information and provides instructions for inventory relocation.
The invoice verification system employs AI-OCR to digitize received invoices, automatically cross-checks them with the core system’s order data, and integrates the payment details into the accounting system.
Mr. Wada shared his reasons for accepting NEC Thailand’s proposal: “None of these systems interfere with the core system. They significantly enhance operational efficiency without imposing substantial costs. In addition to that, I think the fact that we can do so many different things with TALON is very good.”
Achievements After Introduction
Reducing Waste and Redirecting Human Resources to Value-Adding Tasks
Upon consultation with Mr. Wada in December 2020, NEC Thailand proposed a plan in January 2021 and officially commenced the development of the receipt inspection system in March. The system was operational by August of the same year.
Following the positive appraisal of the receipt inspection system, the development of the invoice verification system was initiated in October 2021, and the system was up and running by December 2022. Both Mr. Wada and Mr. Endo provided the following evaluations of the results.
"The receipt inspection system has halved the number of personnel required. This reduction in staff has facilitated a shift towards value-adding tasks that can only be performed by human resources. Furthermore, the decrease in inventory held pre and post-receipt has freed up warehouse space. This has enabled us to eliminate our warehousing costs, which were previously outsourced to an external company. " (Mr. Wada)
"We began by focusing on the invoices from our primary suppliers. This alone led to a reduction in the invoice verification process from approximately 500 person-hours per month to just 200 person-hours. Moreover, after acquiring the necessary skills, we were able to independently develop a system that expanded to include more suppliers. Currently, the system is compatible with 98% of our invoices. This has further reduced the time spent on this process to under 100 hours." (Mr. Endo)
In light of these achievements, the third Kanban System is currently being developed. This system aims to prevent overstocking by triggering orders to suppliers once the inventory of parts and other items falls to a specified level. Previously, the remaining quantities were manually calculated, and orders were placed accordingly, but this method was labor-intensive and could only be applied to a limited number of suppliers. By automating this process, we anticipate a substantial increase in the number of suppliers we can work with.
Contribution to Sustainability Promotion
As climate change and other pressing issues come to the fore, there’s an increasing recognition that responses grounded in ESG (Environmental, Social, and Governance) principles are vital for fostering sustainable growth in management.
In light of these circumstances, Pioneer is taking a company-wide stance on sustainability. The introduction of the new system has eradicated the need to print 5,000 sheets of paper monthly, transitioning the company to a paperless operation. Moreover, the system has liberated Pioneer's workforce from mundane tasks, enabling them to engage in more creative business and enhancing their job satisfaction.
“I take pride in our contribution to advancing sustainability within the Pioneer Group,” states Mr. Endo.
Mr. Wada shared his future aspirations and his expectations to NEC.
“We’ve received word from NEC that they can swiftly react to situational changes by employing AI to restructure production plans and the like. We greatly appreciate NEC’s efforts in keeping us updated on such technological progress. As we aim for continuous growth, we eagerly await NEC's ongoing updates and recommendations.”
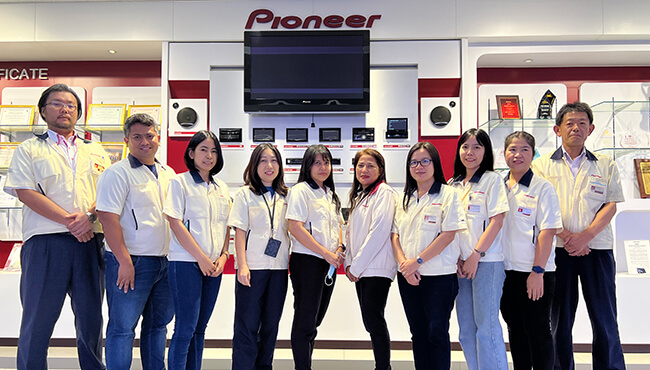
Insights from an NEC Member Involved in the Project
Proposing Solutions to Rapidly Adapt to the Customer's Environmental Changes and System Modifications
Pioneer’s subsidiary in Thailand had been utilizing a core system, which was continually modified and enhanced by their own IT department or with the assistance of a systems integrator. In recent years, the company’s IT department has been persistently overwhelmed due to the high volume of demand. We recognized that this made it challenging to implement swift modifications, hindering progress in boosting operational efficiency.
Amidst these circumstances, we were approached by Mr. Wada regarding a new receipt inspection system. We promptly considered the use of low-code development tools, which were gaining popularity at that time. This was because it would enable us to construct a full-fledged system without the necessity for extensive programming as in traditional system development.
However, since system design and programming were still needed, we decided to initially offer full support for the development aspect of the system, followed by phased skill transfer. Ultimately, the client would have the freedom to modify and develop the system independently.
This approach was particularly relevant because Pioneer, a provider of car electronics products, is a global company engaged in the fast-paced automotive industry. In such an industry, the environment changes rapidly, and system requirements must adapt quickly and flexibly in response to these changes.
The customer expressed their appreciation of our approach, which avoided interfering with their core system—a situation that would have been both costly and labor-intensive. As a manufacturing company, NEC takes pride in our ability to make proposals grounded in our own production site experiences. We believe this is a key factor in the client’s trust in us.
We are committed to continuing to provide beneficial solutions to assist our customers in addressing their business challenges and adapting to environmental changes, which we regard as our value proposition.
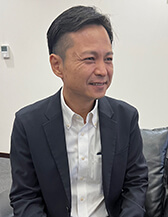
Manufacturing & Automobile Solution Division
Senior Manager
Shigeru Matsubara